Hand pumps have been the go-to solution for field calibration for decades, providing a reliable means of generating pressure for calibrating a wide range of devices from pressure gauges and transmitters to pressure switches and other pressure instruments. But as technology continues to evolve and the demand for higher levels of precision and efficiency continues to grow, pressure testing with regulated nitrogen has become a compelling alternative to hand pumps.
Traditional High Pressure Field Calibration

Field testing on pipelines, oil and gas wellheads, hydraulic systems, and industrial processes requires generating and maintaining high levels of pressure above the range of most pneumatic hand pumps. Operating on the principle of fluid displacement to compress oil or water, hydraulic hand pumps can easily reach pressure levels over 10,000 psi with just a few squeezes of the handle, providing a controlled and adjustable pressure output for calibration purposes. But while this method is generally effective, it can introduce inefficiencies that affect measurement accuracy and add time to the testing process.
- Pressure Instability - Calibrating with a hydraulic hand pump requires training and practice, and technicians often struggle with priming the pump, and overshooting and undershooting to compensate for hysteresis or drift. Differences in technique, experience, strength, consistency, temperature variations, and equipment can all cause fluctuations in pressure outputs which introduce uncertainty and compromise the accuracy of the measurements.
- Contamination - Contaminants such as dirt, debris, moisture, or air bubbles are a constant threat in field calibration and can compromise the quality of the hydraulic fluid, leading to inaccuracies in pressure output. Small particles or impurities in the fluid can cause blockages, leaks, or changes in fluid properties, which can affect the performance of the pump and the accuracy of calibration measurements.
- Maintenance Requirements: Hydraulic systems are prone to issues such as fluid leaks, seal degradation, and pump malfunctions, so regular maintenance is necessary to keep a hand pump in good working order. Techs must routinely flush the system and replace contaminated fluid, which is a messy, time-consuming process. Seals, fittings, and pump components must also be regularly checked for wear or damage, and replaced as needed to maintain accurate pressure readings.
Field Testing with Nitrogen - A Better Way to Calibrate
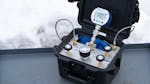
There are a lot of advantages to pressure testing with regulated nitrogen as an alternative to hydraulic hand pumps. It’s cleaner, more efficient, provides a far more stable pressure output, and it’s not as affected by fluctuations in temperature or altitude changes. Nitrogen pressure control devices provide an instantaneous pressure response, with finer level of precision, and can maintain consistent pressure from zero all the way to the full pressure of the DUT. And without oil or hydraulic fluid, there’s no priming, pumping, flushing or purging to mess with. The mechanical components are also simpler, with fewer moving parts. Routine checks for leaks, valve functionality, and cleanliness are usually all you need to keep nitrogen control devices in good condition.
Clean, Stable Pressure Control
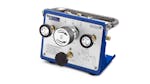
Compressed Gas Volume Controller
Until recently, this type of regulated nitrogen pressure control was common only in lab settings. Our Compressed Gas Volume Controller is a great example, letting you connect to a regulated nitrogen tank easily, and featuring a proprietary fine-adjust piston, fill, balance and vent valves, and a handy stand for table-top use, all together in one light weight, compact unit. But the field is a lot less predictable than the lab. Calibration in industries like oil and gas, petrochemical, utilities and energy is frequently required in areas far off road or in high towers, and often in heavy rain and mud.
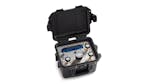
ControlPak
Our ControlPak takes the Volume Controller up a notch by protecting the precision instrumentation in a durable, tactical plastic case that’s made specifically for these conditions. It’s easy to carry in remote locations, and with a wide pressure range of 0.03 psi (200 kPa) to 3000 psi (20 MPa), lets you test multiple devices in a single setup, including differential and static calibration, even at very low pressure. Combined with the included Ralston Quick-test™ connections, hoses, and reference gauge adapters, the rugged ControlPak includes everything you need for fast, precise control over a regulated nitrogen source.
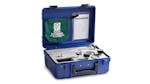
NitroPak
And to take things one step further, our NitroPak has the same precision instrumentation and rugged mobility, but includes an on-board nitrogen cylinder that can hold enough gas for a day’s worth of testing or more.
Fluid-Free Testing
Overall, while hydraulic hand pumps are generally effective in generating pressure for field calibration scenarios, the potential for human error and the use of hydraulic oil introduce the potential for inaccuracies that can be avoided using nitrogen. If you’ve ever been frustrated with pressure stability issues or the amount of time it takes to prepare and clean up after a pressure test, it might be time to try field testing with nitrogen.
We’re here to help!
For questions about any of our compressed gas control devices or any of our pressure calibration products, give us a call at 800.347.6575, contact us or get a quote today!