Natural gas is a vital component of the world’s supply of energy. We use it to generate electricity, heat buildings, fuel vehicles, cook food, power industrial furnaces, and much more. Thanks to substantial technological improvements and increased regulations over the years, it is obtained and transported more safely and efficiently today than ever before. But when gas leaks do occur, they can pose serious health threats, from carbon monoxide poisoning to fires or even explosions. Ensuring that gas distribution lines are installed and operating correctly is crucial, and one of the best ways to prevent leaks is for pipelines and gas distribution companies to pressure test their lines.
What is a Pressure Test?
Pressure testing is the practice of subjecting pipes or pipeline systems to pressure far above operating pressure to confirm their integrity and locate weaknesses in the pipes, fittings or joints. These tests may be done using pressured air, gas, or water, depending on the situation. Pressure testing may occur either before the pipe is put into service or on existing lines that have been in service for many years.
How to Perform a Pressure Test on New Gas Lines
Before a gas line can be brought online, gas utility companies must conduct a pressure test of the newly installed gas line to ensure that the materials, design, fabrication, and installation practices comply with the local codes. All new transmission, distribution, and service lines must be pressure tested before they’re put into service, and the practices are different depending on the type of line. For example, hydrostatic pressure testing, often used for transmission lines, is a large-scale process that involves filling the line with water, pressurizing it to 1.5 times the maximum allowable operating pressure, and then monitoring it for 6-8 hours to ensure that the pressure holds. On the other end of the spectrum, the test for service lines usually takes under 30 minutes, and if the volume is less than 500 cubic feet, then a simple 10 minute test is usually acceptable. To test a service line installed in a newly constructed home, for example, the builder or installer uses air pressure to pressurize the line. Standard gas line inspections usually require that lines hold 1.5 times the maximum operating pressure or 50 psi, whichever is greater. Typically, if the gas line loses 2 psi from a test of 20 psi on the line, the lines are considered acceptable. If the line loses more than 10% of the pressure, it may have a leak. In that case, the leak must be repaired or parts replaced as necessary, and the test must be repeated. Once the test is complete and the gas pipes have been verified, pressure can be carefully bled from the system and the line can be brought online.
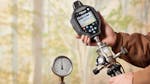
The Importance of Accurate Record-Keeping
While specific test standards differ according to state or regional codes and requirements, accurate record-keeping is a key part of the testing process. Techs must record the beginning pressure, ending pressure, and length of time of each test and any standard analog ASME B40.1 Grade B gauge will usually do the trick. But analog gauges can’t record readings, so the user is required to document the tests with pen and paper, which adds time and opens up a lot of room for error. If they’re not logging pressure by hand, it’s also possible to log the data with a chart recorder. But these tend to be large, clunky devices that use paper charts that have to be scanned and submitted with the report.
A digital pressure gauge like the Ralston FieldLab grants you a lot more control over the pressure testing process. The FieldLab lets you monitor the pressure at any time interval you choose and easily log the pressure drop to determine if the pipe is leaking or not. Along with verification of a valid pressure test it can also record the information required on a Houseline Installation Record (HIR) including the house or plot number, contractor name, and work order. And if a leak test is required, the FieldLab can log the pressure very precisely and provide an output graph of the pressure to include with your documentation.
Pressure Testing for a Safer World
Gas line pressure testing plays an important role any time natural gas piping systems are installed. It helps to identify any design flaws or any weaknesses in the pipe, fillings or joints before the pipe is taken on line, which can prevent gas leaks and potential issues down the road. With the right tools and by following local codes and regulations, pressure testing helps us enjoy the benefits of natural gas safely and reliably.